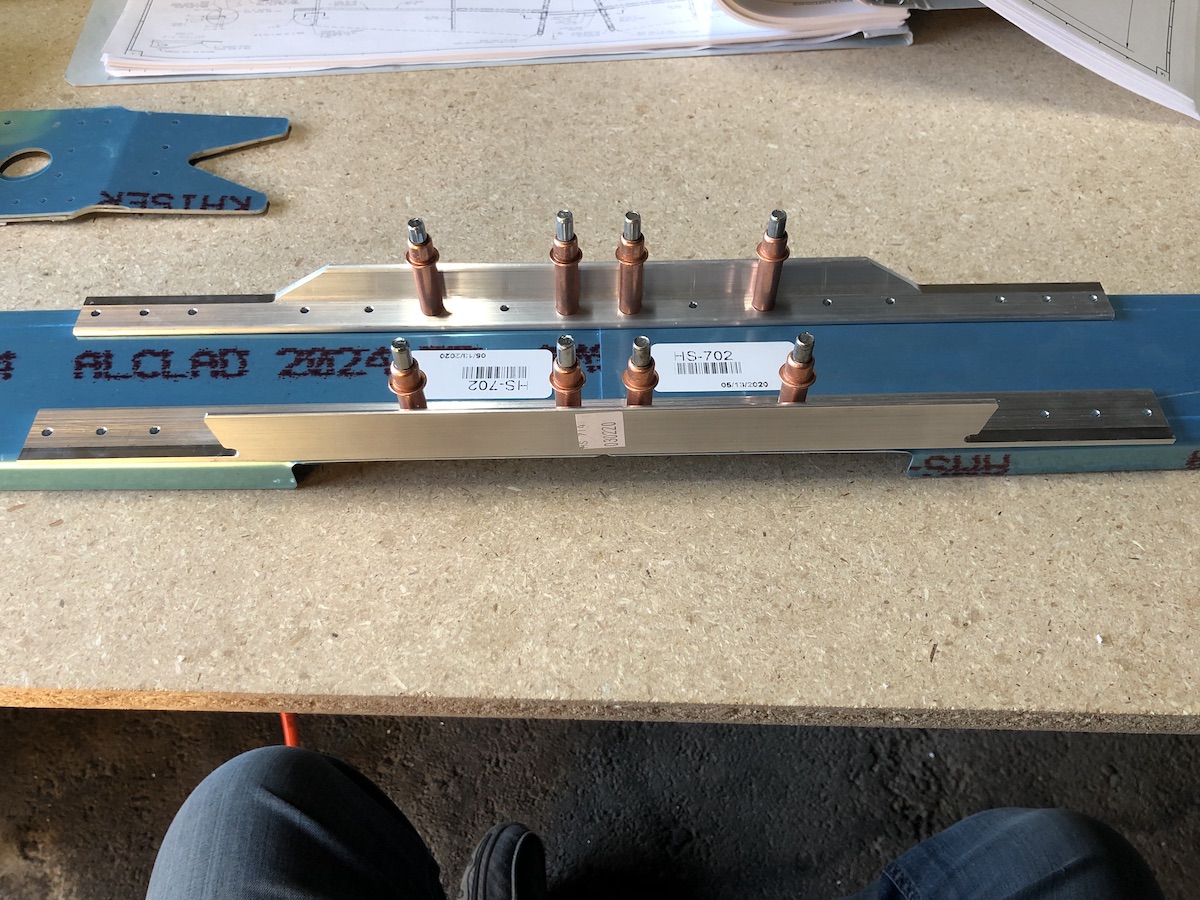
This work was a bit challenging. We started with 2 front spars (HS-702s), and had to make a number of modifications to them in order to build the assembly.
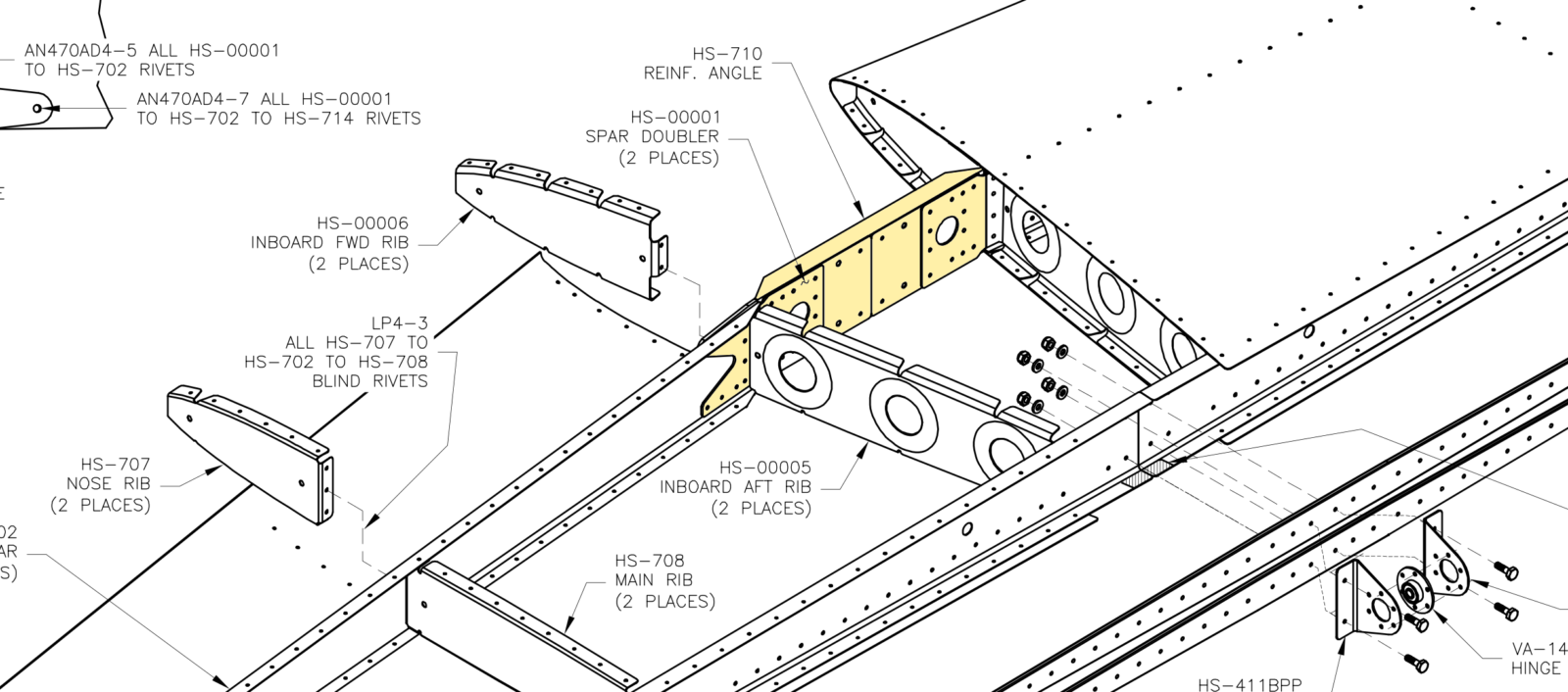
The spars are basically aluminum channels. The raised sides are called flanges. The spars arrived with flanges intact along the whole length. However, we have to trim away a part of the flanges and then create 2 stress relief notches where the trimmed parts will be bent up 6°.
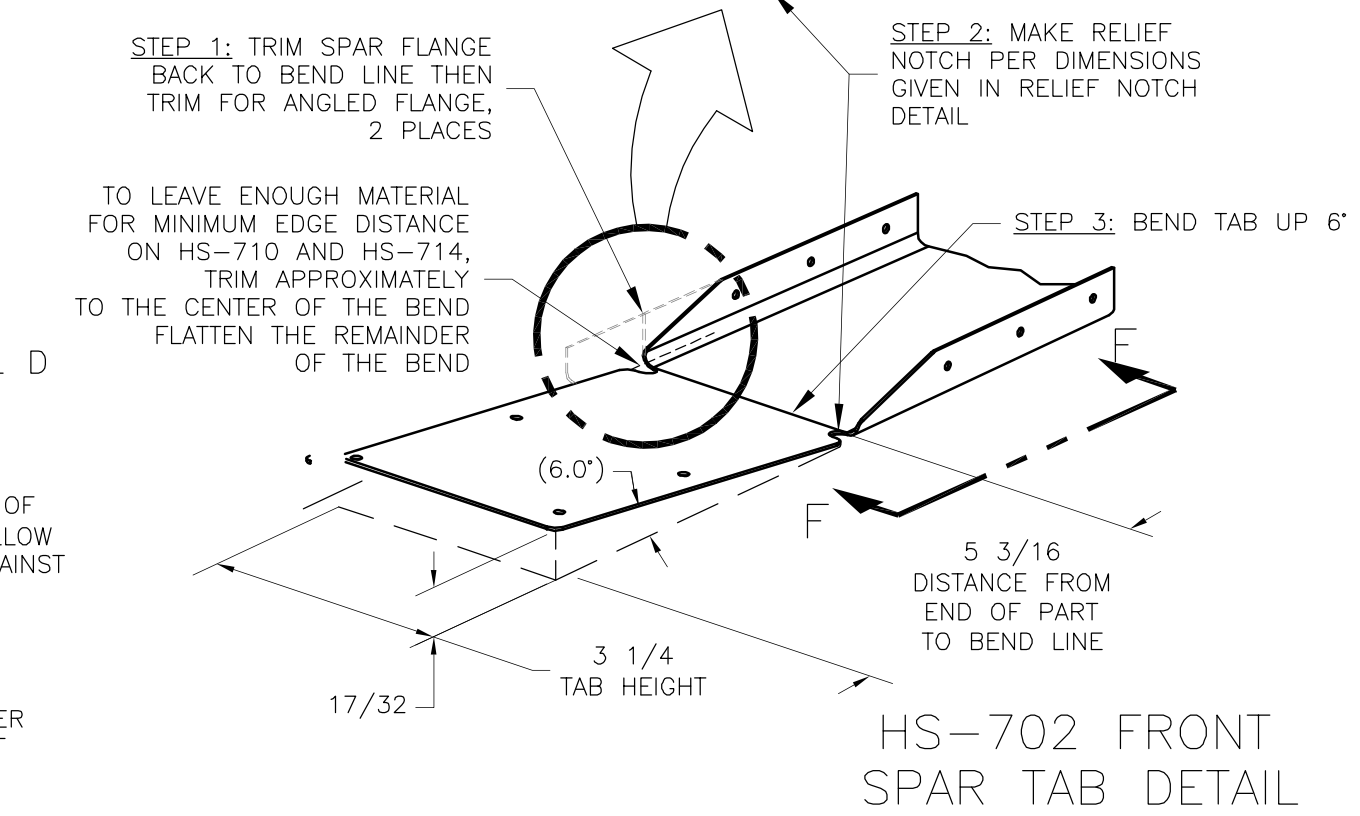
After cutting the flanges, which was done halfway up the bend, the “tab” had to be hammered flat, since half of the bend was left over. I didn’t have a hammer with me, so I used the rivet gun and steel back rivet plate to hammer the edges flat. Turned out pretty well…
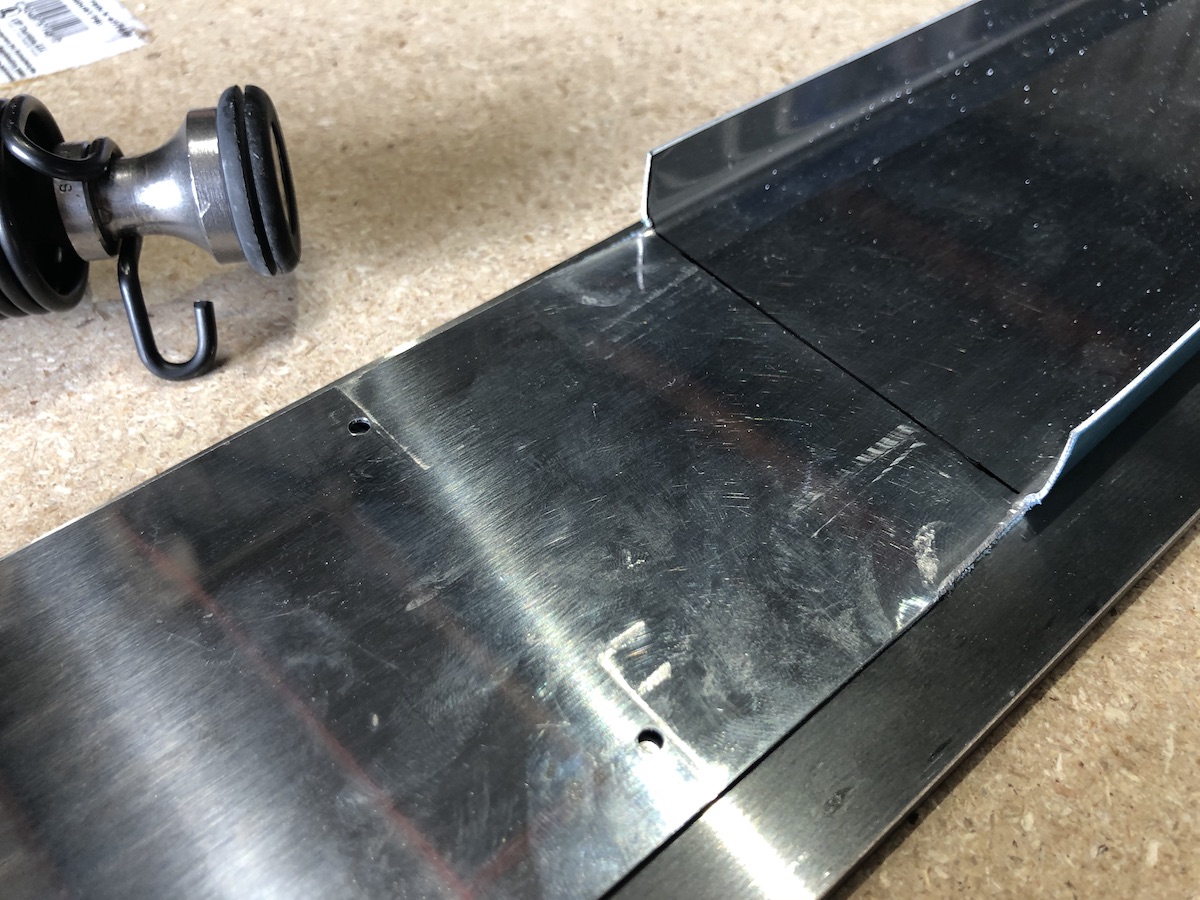
After that, a couple pilot holes are drilled, and then enlarged to 1/4″ using a “unibit”. I tried using the unibit in my hand drill, but that was probably not a good idea. The bit gouged and tore the holes. I later found that this should have been done on the drill press.
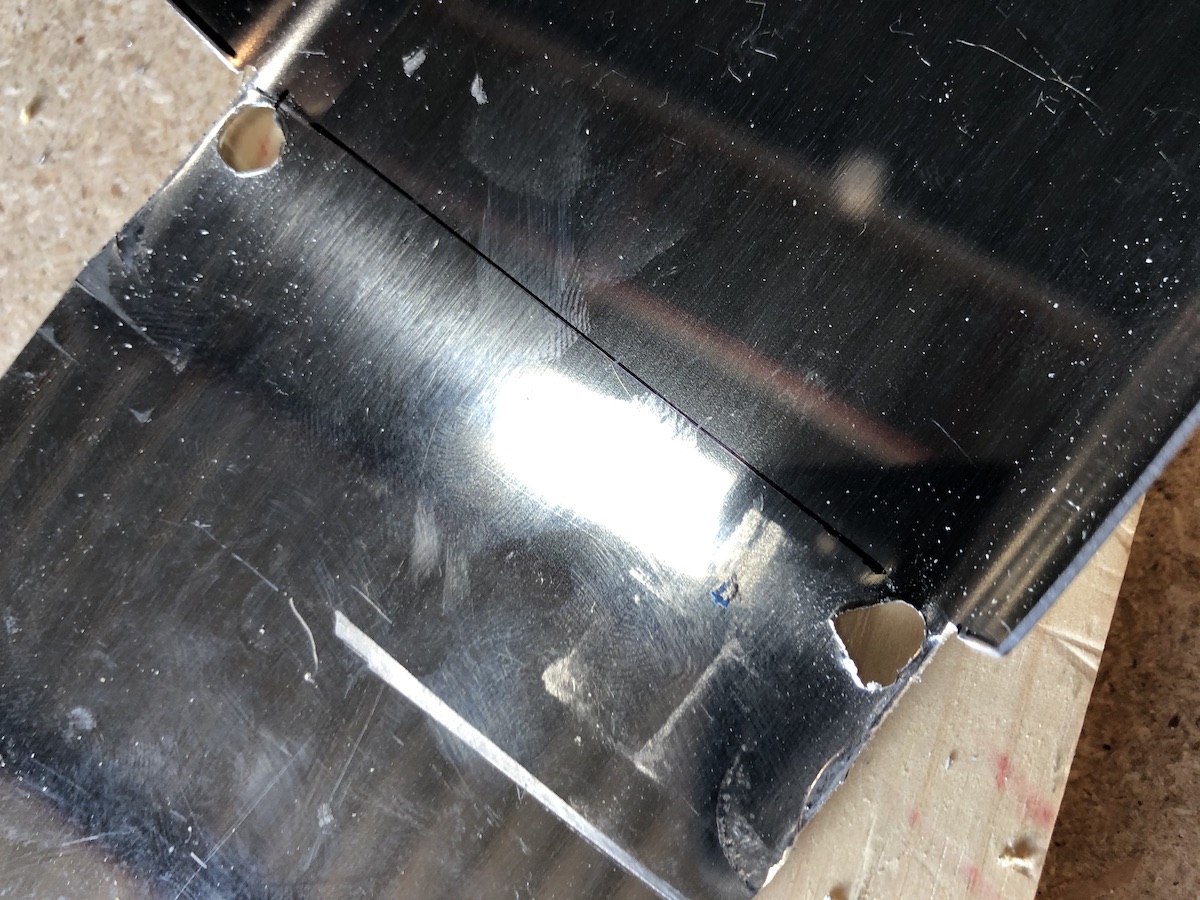
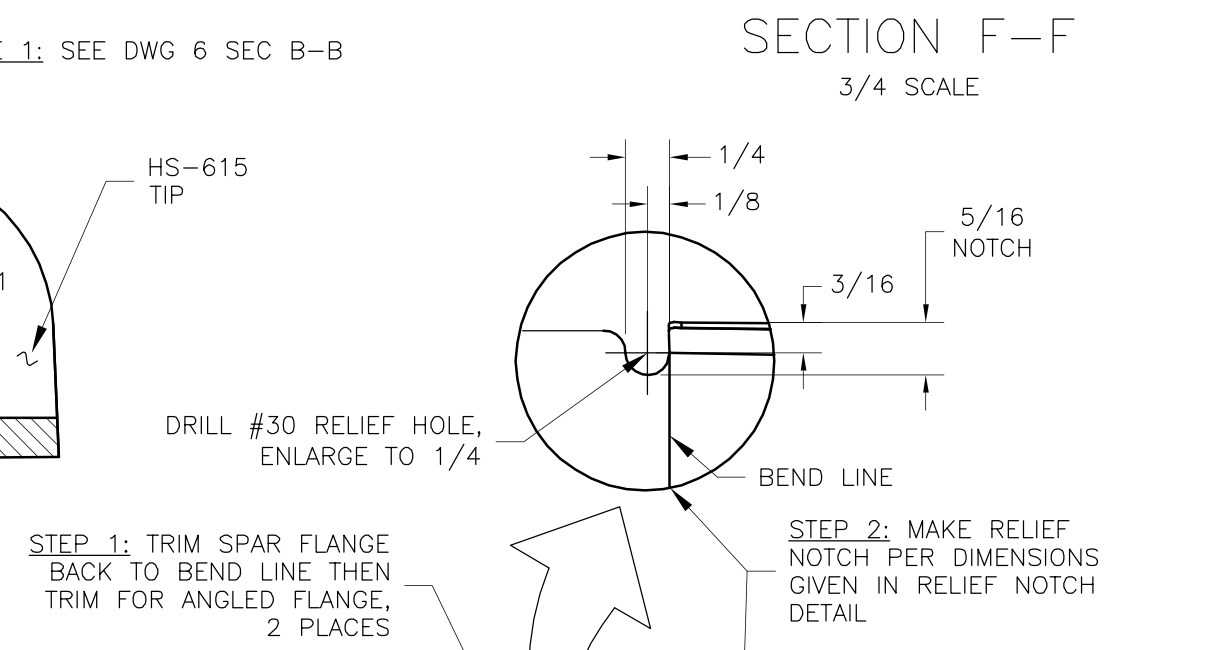
Once these holes were enlarged, we’re supposed to cut them into notches with radii all around in order to avoid stress cracks. Then, the flanges at the bend line needed to be cut back at an angle. We stopped here for the day because trimming the angles in the flanges called for maintaining a “minimum edge distance”, which I couldn’t find on the drawing.